Background Information
Keel was awarded a contract for the Sikorsky-Boeing Joint Multi-Role (JMR) program, a key initiative advancing military rotorcraft. The project involved manufacturing and integrating critical components for the S-97 Raider to meet the U.S. Army’s Armed Aerial Scout (AAS) requirements.
Keel precision-machined solid titanium forgings for the main rotor shaft and hub, upper and lower hubs, and tail rotor shaft. The company’s advanced manufacturing capabilities ensured that each component met the stringent performance and quality standards required for military aviation.
Keel’s skilled engineering team delivered high-quality, reliable parts, contributing to the success of the JMR program and advancing next-generation rotorcraft technology.
Business Challenges
- Raw Material Cost: This project included a great amount of risk due to the expense of the raw material. Each rotor shaft is precision machined from a solid titanium forging that is 7 feet long and weighs 800 pounds. The cost of the titanium forging and the critical application allowed no room for error in the machining operations.
- Schedule: Another manufacturing company had assured the customer they would complete the work, but at the last minute, they could not complete the project. Desperate for a solution, the customer turned to us for help. Despite a near-capacity machining schedule and the risks involved, we accepted the challenge and strived to meet the customer’s project deadline.
- Machining Plan: Developing an effective machining plan for the rotor shafts presented a significant challenge due to the complexity of working with solid titanium forgings. Each shaft required precision machining to exact specifications.
Approach and Solution
Keel took a strategic and collaborative approach to address the machining challenges and project risks. The team immediately developed a detailed machining plan, working closely with the customer to identify and resolve any design issues that could impact manufacturability.
To ensure smooth execution, Keel assembled a dedicated Program Management team and established an 11-month production schedule. By implementing rigorous daily management and maintaining close communication with the customer, the team was able to optimize processes and mitigate potential delays. As a result, Keel successfully delivered the first unit two weeks ahead of schedule, with the remaining six units progressing on time. This success highlights the effectiveness of Keel’s proactive planning, disciplined execution and strong customer collaboration.
Value Delivered
At Keel, we recognize that delivering high-precision, mission-critical components require more than just machining expertise – it demands meticulous planning, collaboration and a commitment to excellence. Our work on this project was not just about manufacturing rotor shafts; it was about ensuring reliability, precision and efficiency in a high-stakes environment.
By developing a robust machining plan, assembling a dedicated Program Management team, and maintaining close communication with the customer, we successfully delivered the first unit ahead of schedule and ensured the remaining units stayed on track. This achievement reinforced our ability to tackle complex manufacturing challenges with precision and efficiency.
Keel’s proactive approach not only met but exceeded customer expectations, demonstrating our capability to deliver high-quality components in high-stress situations. Our success on this project underscores our commitment to innovation, quality and on-time delivery—key factors that set us apart in the mission-critical defense manufacturing industry.
At Keel, we don’t just machine parts; we engineer solutions that drive success.
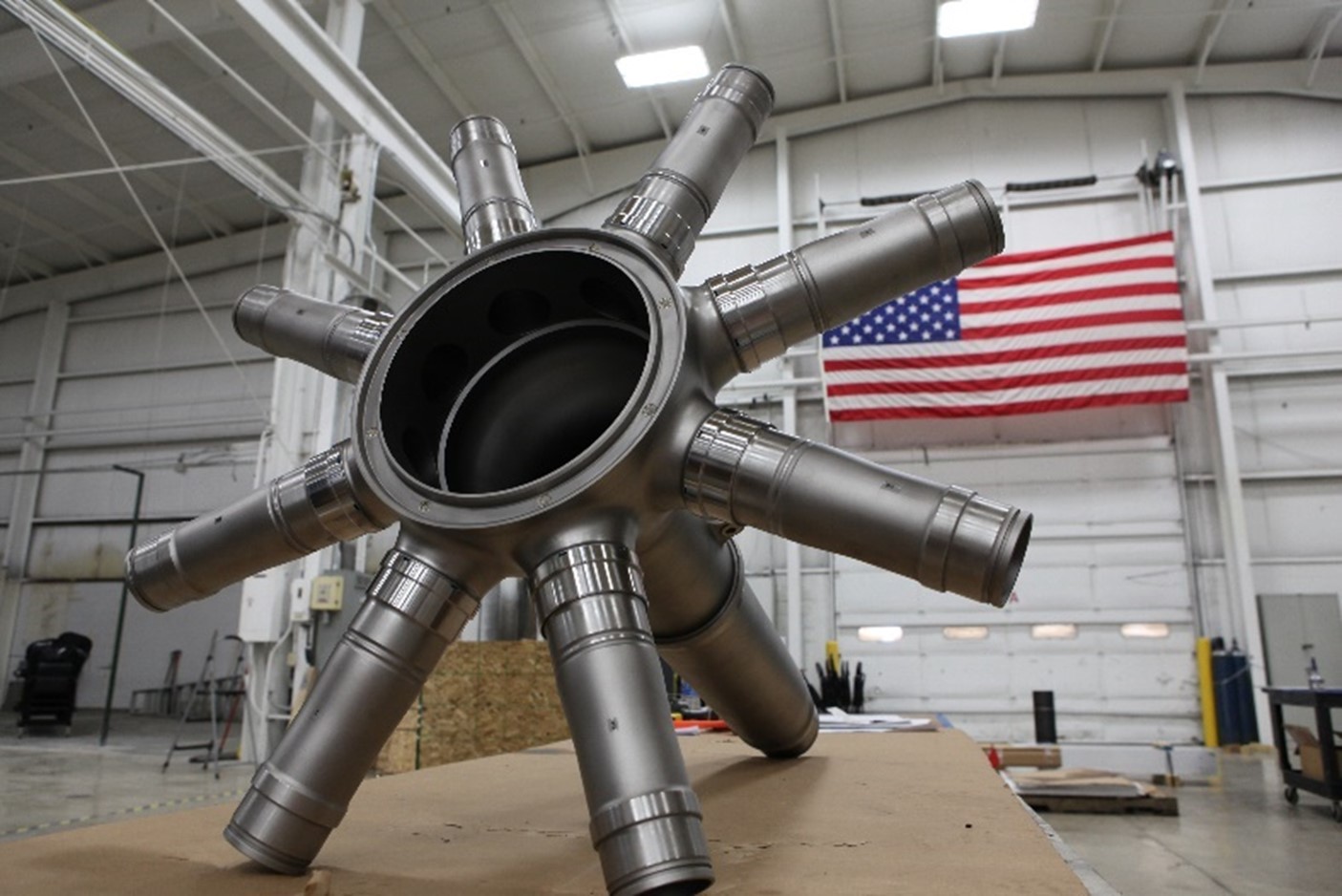