The United States Army needed a shipbuilding partner for the repair of its Landing Craft Utility Fleet (LCUs). After performing rigorous demands of amphibious forces to move equipment and troops to shore, the LCUs needed to be restored and fully operational for future battles.
Keel (Yonges Island) was awarded a contract to repair vessels damaged in warfare. The choice to select Keel as a trusted supplier stemmed from its ability to ship the vessels directly to the facility by water, eliminating costly shipping expenses.
Keel’s machinists, electricians, pipefitters, hull repair specialists, team of American Bureau of Shipbuilding (ABS)-certified welders and Marine Division Manager repaired the first set of LCUs more than 30 years ago. Extensive project knowledge enabled Keel to provide the customer with a cost-effective solution for all repairs needed for the governmental fleet. Our team’s dedication to quality has helped to establish Keel as the principal supplier for vessel maintenance and repair domestically and on-site Zone 3 repairs around the globe.
Business Challenges
- Product Life Expectancy: A vessel that performs for the United States military is mission critical. We deliver to the specifications required to keep the mission at the forefront without room for error. The government approached us with the need for repairs that would enhance the ship’s condition and for services that would extend the life of the product. We needed to implement a comprehensive program that would meet the specifications required by the customer.
- Timeline: Keeping our warfighters safe is always at top of mind for our team. Each vessel must undergo stringent inspection required by ABS to ensure its safety. The customer needed a partner who kept its focus on quality. Any evidence of rust found utilizing Ultrasonic Testing can lead to material removal, stripping or gutting of the vessel, affecting the customer timeline.
- Expansion and Equipment Requirements: Selecting a partner who is experienced in shipbuilding and can accommodate massive platforms is required. When the U.S. government sent us the request for proposal, they needed a facility that could handle the specifications along with the working envelope (size and weight) of the LCUs—in the water and on land.
Approach and Solution
To extend the service life expectancy of the vessel, we have several team members with years of experience who are readily available to machine, perform electrical and hull repairs, and prep and paint to exact specifications.
We have performed specialized ship repair work, including:
- Machining – valves
- Retrofitting with new engines
- On-Condition Cyclical Maintenance (OCCM)
- Replacement of bow thruster & propulsion engines
- Hull and superstructure repairs
- Electrical rework
Our quality team works with ABS to ensure each vessel is classified to standards and technical specifications. Because of stringent quality requirements, it is critical that quality is front and center when performing the scope of work. Attention to detail ensures the turnaround time is met and that a vessel is always available for combat.
As part of safeguarding the vessel, we use Ultrasonic Testing. If readings return low, the material must be removed and replaced. If rust is detected, stripping and gutting must be performed prior to painting. With years of experience and our in-house quality team, we can address these issues proactively, ensuring consistent quality and efficient project completion.
To mobilize the tons of steel these ships are comprised of, we installed a 550-foot assembly area and transfer system, utilize an end launch cradle for barges up to 370 feet by 70 feet, have 1,000 tons of dry-docking capacity and a railway rated at 10 long tons per foot (1,000 tons). For prep and paint, we implemented a 7,000-square-foot facility with two 100-foot by 35-foot by 20-foot booths and are planning to expand our paint facility.
With our dedicated and knowledgeable staff, navigating through trials and tribulations, Keel became the leading partner who could provide service to the scope of work determined by the condition of each vessel after battle.
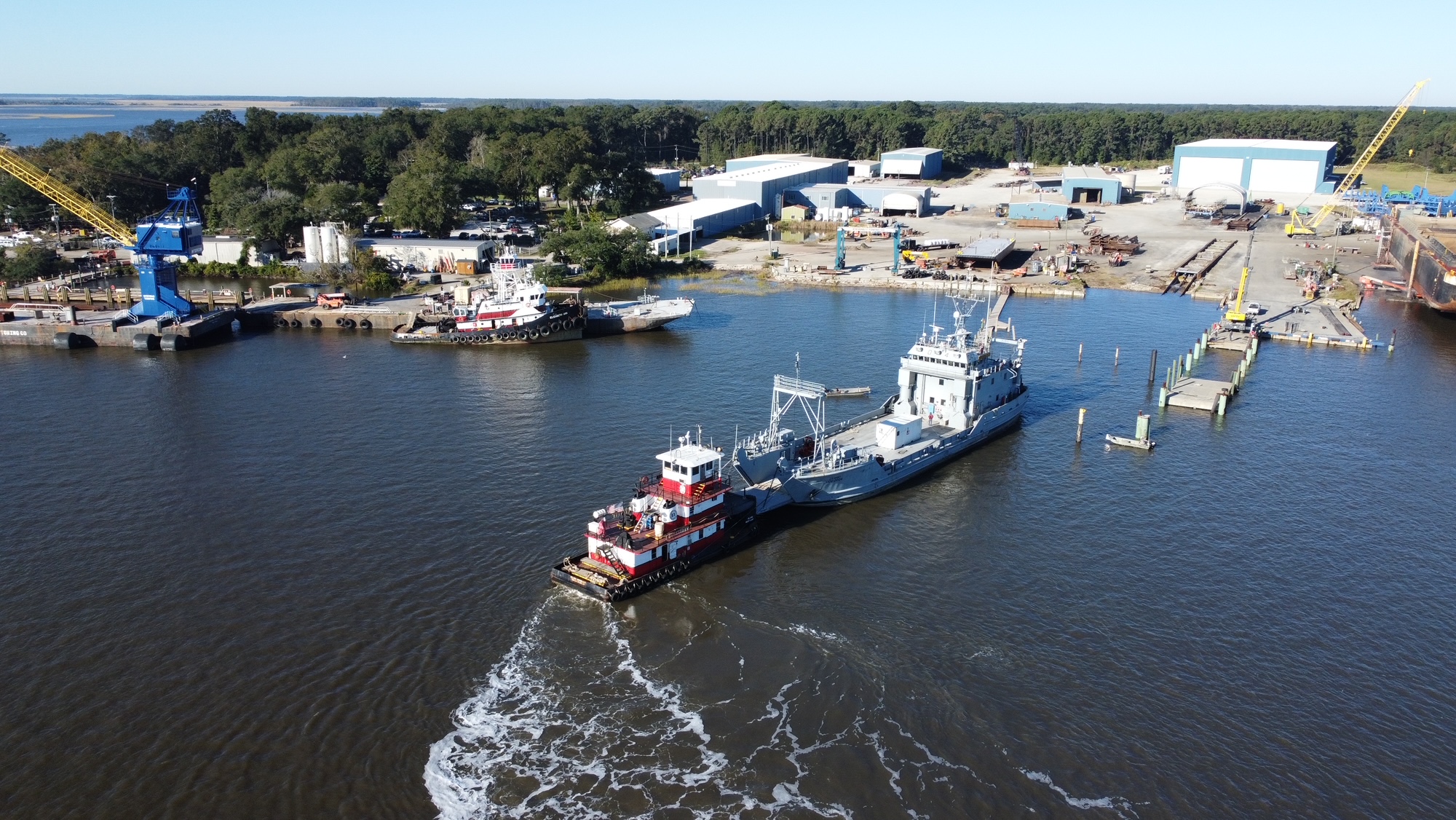
Value Delivered
The lives of our service men and women are irreplaceable, so we make it our mission to bring to market the best quality products that provide protection in the most rugged environments. Value to us is not only about offering end users peace of mind for their protection, but also having the facilities, equipment and dedication to solving customer challenges to ease the burden. We pride ourselves on the ability to provide a customer-focused approach through every step of the project. Project-specific Program Managers ensure the project is on schedule and provide detailed reporting, allowing our corporate partners to rest assured that Keel will tackle the job. Whether via weekly meetings or working directly with the customer on site, we can proactively identify challenges to minimize the risk of extended downtime.
Our customers can count on us for ample space, cost savings and the highest level of quality possible to complete their ship repair needs. At our Yonges Island facility we have abundant frontage on our deep-water access point to accommodate four vessels for full-rate production. The water frontage enables us to reduce shipping costs as vessels requiring emergency repairs can be easily transported by water to Yonges Island. By reducing shipping costs, we can reduce our customer’s overall costs significantly.
When mission-critical vessels are needed in action, Keel is the trusted partner with a proven track record to ensure they are fully restored and certified to combat-ready status. We are Keel, and what we build, builds us.